Risdon
Risdon - The Beauty Manufacturer
In 1910 Naugatuck’s citizens were dependent on the rubber industry for the prosperity of the town. Seasonal layoffs in the rubber industry proved a hardship for citizens, as well as, the town’s economy. A decision was made at a January 1910 Town Meeting ”to endeavor to bring new industry to town”. By the end of the meeting, $25,000 was pledged by one hundred and fourteen citizens to form a manufacturing company. They ultimately decided to purchase a faltering tool works in Waterbury known as The Risdon Tool and Machine Company.
The company’s very first products were eyelet machine tools and clock maker’s tools, used to shape gears and sprockets. Then they began producing safety pins. Local housewives and children were often hired to attach the pins to cardboard for easy sale.
By the 1980’s Risdon had become the premier manufacturer of packaging for cosmetics. Producing and perfecting lipstick tubes for Chanel, Revlon, Estee Lauder, Clinique, and Avon. At one time, it was estimated that Risdon produced 95% percent of the lipstick tubes on the market. At one point, the company reported they were sending a truck a day to Revlon. Over the years Risdon employed many prominent Naugatuckians such as Lewis Dibble, Donald Tuttle, and Charles Brust.
Risdon closed in 2009.
The Risdon Story – 100 Years Later
By Bridget Mariano
On a winter night in January 1910, 114 Connecticut citizens gathered at Naugatuck Town Hall and raised $25,000 to support a bold new manufacturing venture. The company they backed—The Risdon Manufacturing Company—would become a hallmark of innovation and resilience in the Naugatuck Valley.
As described in Connecticut Enterprise (1960), “The story of the Risdon Manufacturing Company tells of small beginnings, financially and physically. It is a story of high hopes and a little Yankee ingenuity and tenacity.”
Source
Naugatuck Historical Society Newsletter
Volume 15, Issue 1
January - February 2010
Excerpt from Naugatuck Daily News – Saturday, August 31, 1946
World War II - History Edition
Risdon Took Only Six Months For Conversion To Wartime Production
Incendiary Bomb Assembly, Percussion Primer Important Items
Conversion from peacetime to war production extended over a period of about six months at the Risdon Manufacturing Company, when the firm was placed on a full production war items in full production in 1942.
The safety plunger assembly used in the CWS incendiary bomb and the MK-19 percussion primer were the principal items produced by the Risdon plant. Other war products manufactured were primer parts, fuse control, instruments, and aircraft items. Among the textiles manufactured were tent, clothing, boats, and miscellaneous canvas and duck items used by the Army, Navy, and Marine Corps.
The Risdon plant also contributed to the development of new products. It converted part runs made from solid metals to stampings, and converted parts made in two pieces to sheet metal. It also made conversions to save critical war materials.
The firm's representatives aided in the capacity of consultants to the War Production Board to effect changes in metals to release critical materials. Wires were redesigned for ordnance, radio, radar, and aircraft to save critical man hours and materials.
Through additional jobs and personnel training, the plant was enabled to both increase production and save labor and material, when both labor and material became increasingly scarce. Extra employees and supplemental workers were used to aid in maintaining production schedules.
For its efficiency of operation and the contributions made in saving labor and materials, the Risdon Company was awarded the Army and Navy “E” on Feb. 20, 1943. The firm also received the Treasury star for its record in the sale of bonds and stamps.
The company cooperated with the Ration Board in formation of transportation committees to organize car-sharing groups and save gasoline.
Excerpt from Naugatuck Daily News – Monday, September 15, 1947
Industrial Exhibit Supplement
Three Plants Operated By Risdon
4,000 Metal Parts, Products Made in Local, Danbury, Waterbury Units
The story of our start in the metal fabrication business begins with the fact that Naugatuck was probably the only community where property—being close to the center of town—offered an ideal location for the organization of a factory in the business of fabricating diversified metal items. This diversity of interests, unusual in the trade, has enabled the firm to manufacture thousands of different metal articles, contributing more to the training of men than to the manufacture of any one item.
The assets of The Risdon Tool & Machine Co. were acquired in 1909, and the double building located on Waterbury road was purchased. Ten thousand dollars was paid for the entire plot and buildings. It was decided at that time to make this the site of the future operations of the manufacturing of metal products, and the corporate name was changed to The Risdon Tool and Machine Company.
Since Naugatuck assumed a wider interest in the borough’s industrial growth, we started construction of the first building of our present plant early in 1913 on ground given by George Andrew. He was one of the first interested in the diversification of Naugatuck’s industrial interests.
On March 17, 1913, we moved from Waterbury to the new building which had 6800 square feet of floor space. At that time we had 15 employees and 25 machines. Our first metal fabrication job in the new location was the making of metal easter eggs. As one year succeeded another our industrial growth was steady, consistent and healthy. In 1915, 1210 square feet for plating and packing departments were added to the original factory.
New Additions
The years 1916, 1917, and 1918 brought new additions for a tool and press department, larger office space, and a new freight shipping plant. This new building was completed in the record time of 43 days. It was formally opened on April 27, 1918. During this time the corporate name was changed to The Risdon Manufacturing Company.
From time to time space was increased so that today we occupy 70,000 square feet of floor space at Naugatuck alone and a combined total for all plants of about 150,000 square feet. This affords an interesting comparison with our original plant space of 6800 square feet. One reason for this growth is our accomplishment in replacing longer, more costly methods of metal fabrication with automatic processes.
Our product diversification was widened by the purchases of the assets of the following companies: Remo Manufacturing Company, Smith and Griggs Company, The Consolidated Safety Pin Company, and a new factory established at Danbury.
Danbury Plant
This youngest plant of the Risdon family has developed, since its start in December 1943, into a substantial and increasingly active unit. The employees at the time of its first birthday numbered about 150. The management and production policies that have signaled the success of our metal stamping plant at Naugatuck and our wire products plant at Waterbury are reflected in the operation of this cosmetic container plant at Danbury.
Risdon’s reputation for quality-made products has already extended to most of today’s leading brands of cosmetics. Our list of customers reads like a “Who’s Who” of the toilet goods industry.
Our steady and consistent growth is prefaced by a policy of under-expansion rather than over-expansion. Thus we have never been in the position where we would have to take work as an overhead carrier, or on a theoretically less-cost basis to keep up shop production. Our business with employee lay-offs have been kept to a minimum. To further this policy we have accepted only legitimate business of definite long-term production value. Our automatic equipment and the high cost of tools require such a policy. Since we have never accepted or solicited any business from anyone whose credit is questionable, we have almost entirely eliminated credit losses.
We have always seen to it that financial resources have been adequate. No expansion was started or obligations incurred unless we had sufficient capital. For this reason we are, and always have been, financially sound.
Our first dividend was declared in 1916, and since then we have never passed a declaration period. We owe the high standards of our financial policy to the late George T. Wigmore, our secretary and treasurer, who was associated with us from 1910 until his death in 1936.
The foundation of our business is the production of metal components—small metal parts and assemblies of parts that are of great importance to industry and to everyday life. Whether it is a ferrule on your pencil or a metal clip for your key case, wherever your roving eye comes to rest, you are likely to glimpse a metal component performing a useful function.
4,000 Products
In a prominent place in our engineering department are two large star-shaped sample wheels on which are displayed, for easy and quick reference, all of our 4000 different parts or products fabricated from metal in our Naugatuck, Waterbury, and Danbury plants.
Here in our engineering department the circle of production starts and ends—the solving of the problems of tooling, fabricating, and finishing—the testing of materials—the control of uniformity when repeat orders are received. Under the guidance of experienced engineers, production moves smoothly and rapidly. Frequent conferences are held between the engineers and management executives to smooth out production wrinkles.
As an example, let us consider the art of metal drawing, called by some metal stamping. Here is a process by which sheet metal fed into a multiple plunger press is first blankstamped into circular or irregular blanks of varying sizes. Then, by a series of plungers, the discs are cupped in progressive steps until the shape of the finished object is finally accomplished. As the shapes vary in size and detail, the number of plunger steps are likewise varied.
When we pause and consider the stamping machine, we find that, when properly equipped, its action of stamping and drawing is automatic. Yet back of this machine and its powers lies human and almost superhuman skill—skill of the product designer, skill of the machine toolmaker, and skill of the finisher. This is equally true whether production is done on a multiple plunger press, slide press, power plunger press, or wire forming machine. Here at Risdon such skills have been the cornerstone of our success in the making of metal components and wire goods.
As a result of our study of metal-formed products, their uses and functions and processes of production, we have in a great many cases effected considerable savings in metal, in production time, and in overall costs. Parts that were previously made by slower or more costly methods have been found practical to make on our multiple plunger presses in one continuous operation.
Handling Difficult Work
Simplification of procedures, speeding up of work output, cutting of metal waste, lowering of production costs—these have been the outstanding contributions to the automotive, electrical and other manufacturing industries. And these fields have provided ample evidence that sheer metal reduction of many parts has marked a decided conquest over other methods. We have put to work all of the methods of automatic metal drawing which have enabled us to meet more than 90 percent of our problems. More than 90 percent of our production involves the alteration of sheet metal into shapes extremely difficult to make.
The crudely formed metal objects of yesterday are obsolete by today’s standards. We speak now of neat items of tolerance in less than .00025 inches. There is no room for guesswork. Accuracy in every detail has become important in importance.
Our first automatic multiple unit press of more than twenty-five years ago is still in active operation. Today we have batteries of newer and larger machines with greater capacities for performing additional or supplemental operations. World War II uses of this type of machine contribute greatly to our progress and growth.
A total of 35 million cartridge clips was made at no substantial savings over the previous method of manufacture. In addition, Colt Automatic 45 cal. pistol magazines were made in World War I and again in World War II—striking example of the continuity and stability of our company and its production operations.
As in our metal drawing factory, so at Waterbury accurate operation is the keynote of our safety pin manufacturing. Equipment used by us at Waterbury for this function is the keynote of our safety pin machines having been designed by our own engineers and built in our own shops. They are fully automatic, and are exceptionally high speed, and their complex mechanical motions necessitate an intricate and delicate balance of moving parts, such as cams, levers, gears, etcetera.
Large varieties of styles and sizes of safety-pins are made on this equipment with modification of dies, such as guard and shield (both inside and outside) examples of all safety features as exemplified in our Duplex and Safepoint lines. A thought that safety pins used mostly by women brings us to our latest line:
Lipstick Cases
A feast for feminine eyes is afforded by the lipstick cases and cosmetic containers made by Risdon. Their construction and finish mark the perfection of the designer’s art.
More than pleasing to the eye, our containers must be correctly made. Parts must fit perfectly and function smoothly.
To see the metamorphosis of sheet metal into these auxiliaries of beauty, we must visit a department in our Naugatuck plant. Here we notice multiple spindle presses stamping out circular or irregular blanks from sheet metal and then step by step forming tube-like cases and covers for lipsticks and containers for rouges. There, too, we see machines turning out the parts for the lipstick propelling and repelling mechanisms.
Now our secondary operations at Danbury enter the production picture. The very important finishing is then performed. Next, employees on the assembly lines set the mechanisms together, insert them in the cases, and put on the covers. Then comes final inspection prior to packing the finished article for shipment.
From the time that our engineering and development departments start on a new and different problem of production, an unusual type of industrial psychology enters the picture. Our work planning never takes for granted that a job can’t be done simply because it hasn’t been done. We seek—and find—new ways.
As a result the Risdon designers and machine toolmakers, because of their long experience and great technical ability, are often able to conquer the seemingly impossible. They have often proved that what formerly could not be done can be accomplished by vision, ingenuity, and skill.
Know Jobs
In all three of our plants, at Naugatuck, Waterbury, and Danbury, our management and our entire personnel know their jobs to an unusually thorough degree. As toolmakers and diemakers we employ only specialized craftsmen who are well-trained, efficient, and versatile. Technicians and machinists, correct engineering and ample facilities, a background of knowledge and a reputation for ingenuity—these are among the assets of any branch of Risdon service.
Our policy has always been, and still is, to build up our personnel when a good man is available rather than to wait until there is a definite need, whether he be an executive, an engineer, or plant employee. “A company consists of the people who are in it” and we are proud of our large, happy family of faithful workers.
No history of Risdon would be complete if it did not pay tribute to the man who is primarily responsible for its enviable growth. In 1913 Lewis A. Dibble came with the Risdon as manager, in 1917 he was made vice-president, becoming president in 1927. From his advent the growth of the company has been steady and rapid. Gifted with boundless enthusiasm, unusual foresight, mechanical insight, and being a born leader of—men, he has raised Risdon to the heights. His ability was so outstanding that his services were sought as president of the Eastern Malleable Iron Company, and as director by such companies as the Connecticut Light and Power Company, the Torrington Company, Bridgeport Brass Company, and C. Cowles and Company of New Haven. Under his guidance, Risdon should continue to prosper and grow.
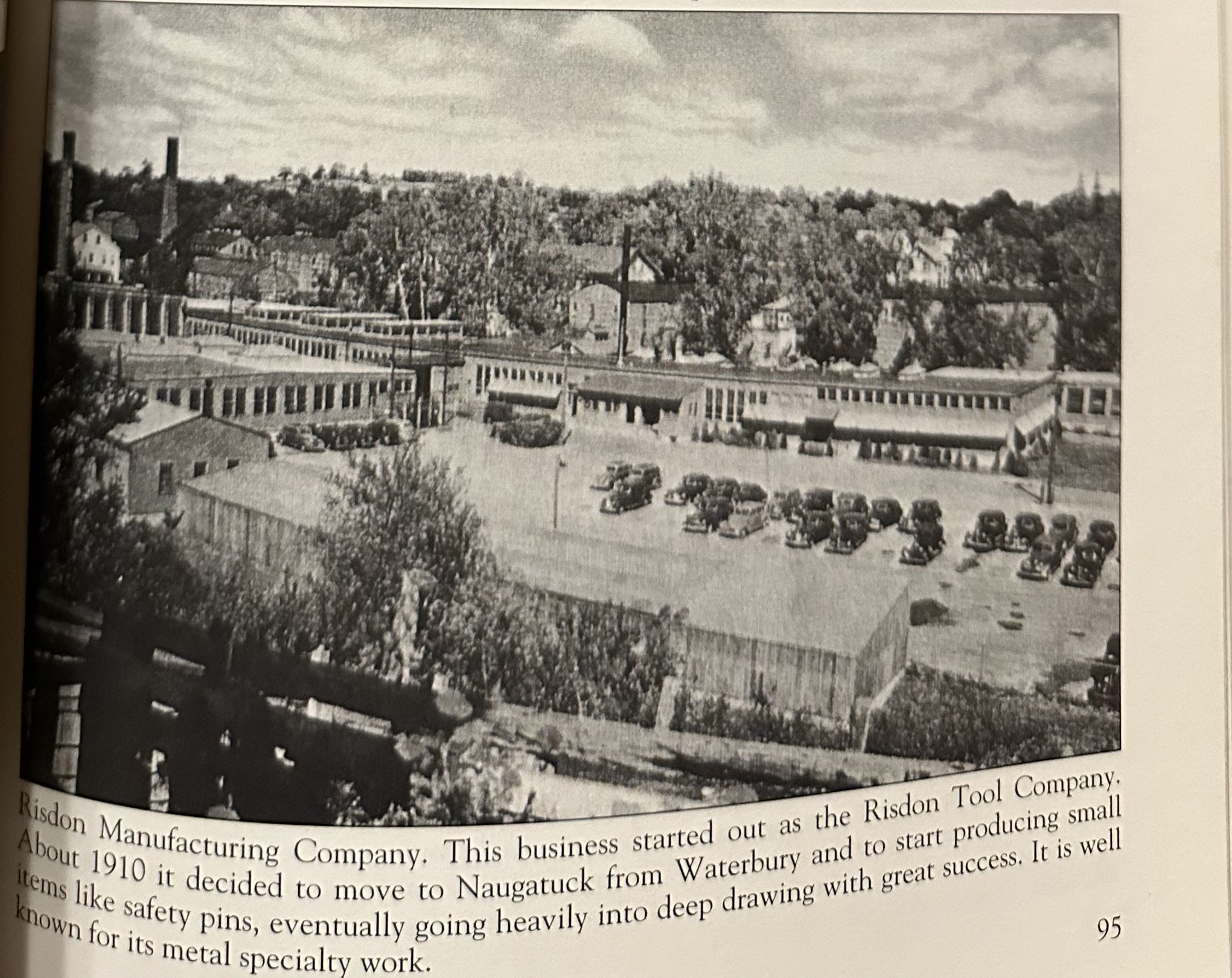
Images of America - Naugatuck & Naugatuck Revisited Dana J. Blackwell and The Naugatuck Historical Society (November 1, 1996) Ron Gagliardi (August 25, 2004)
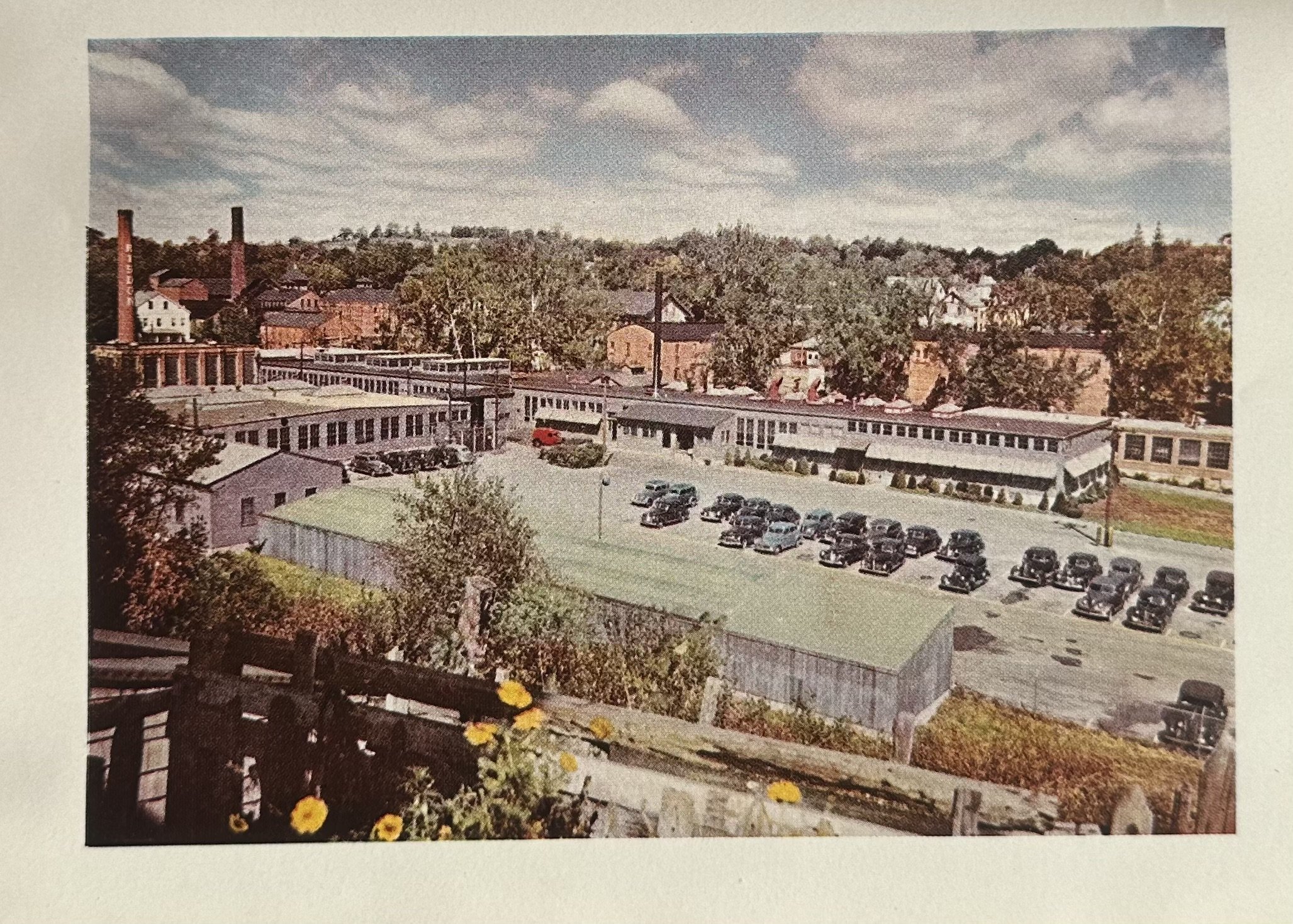
Source: Connecticut Enterprise - Risdon
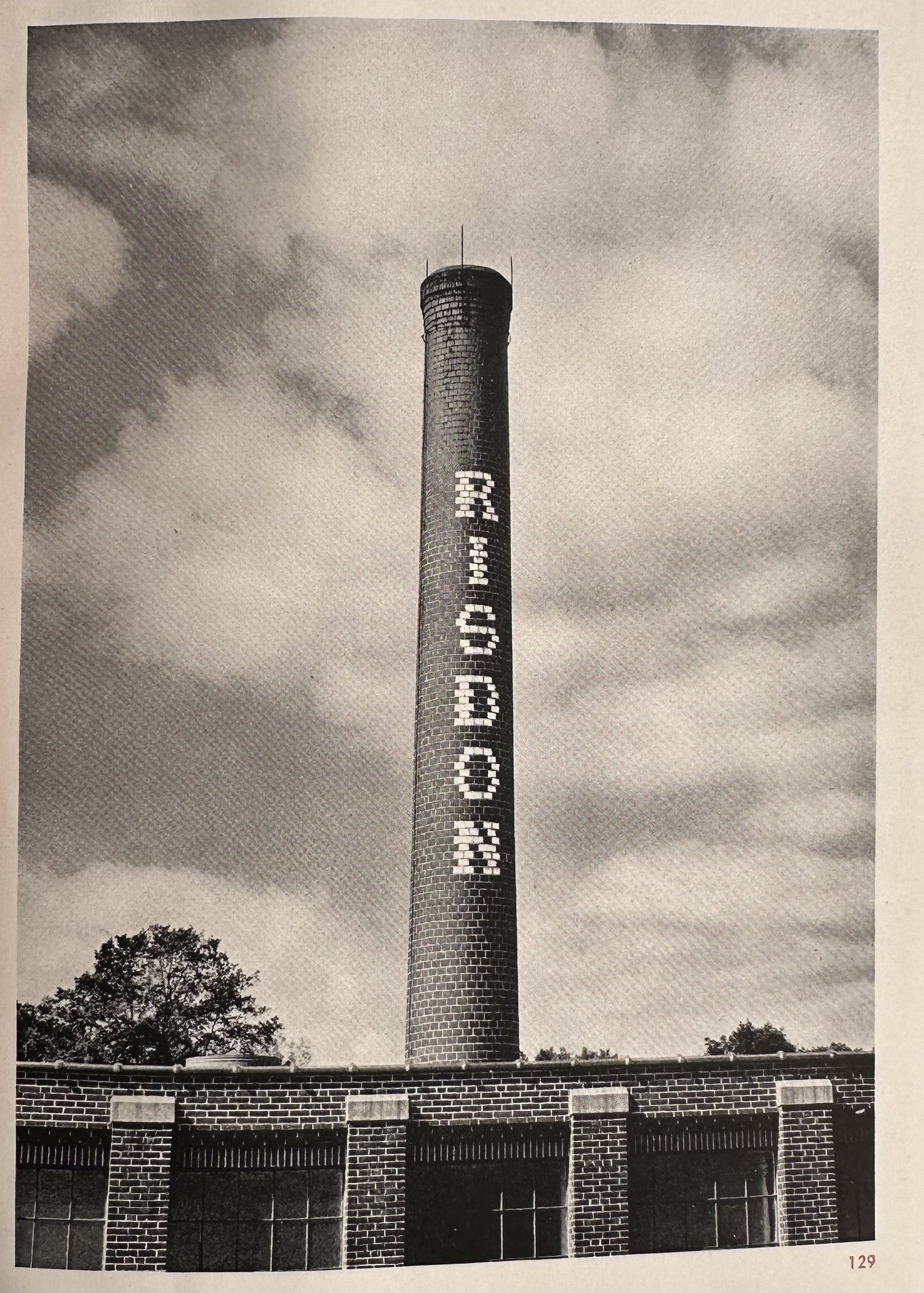
Source: Connecticut Enterprise - Risdon
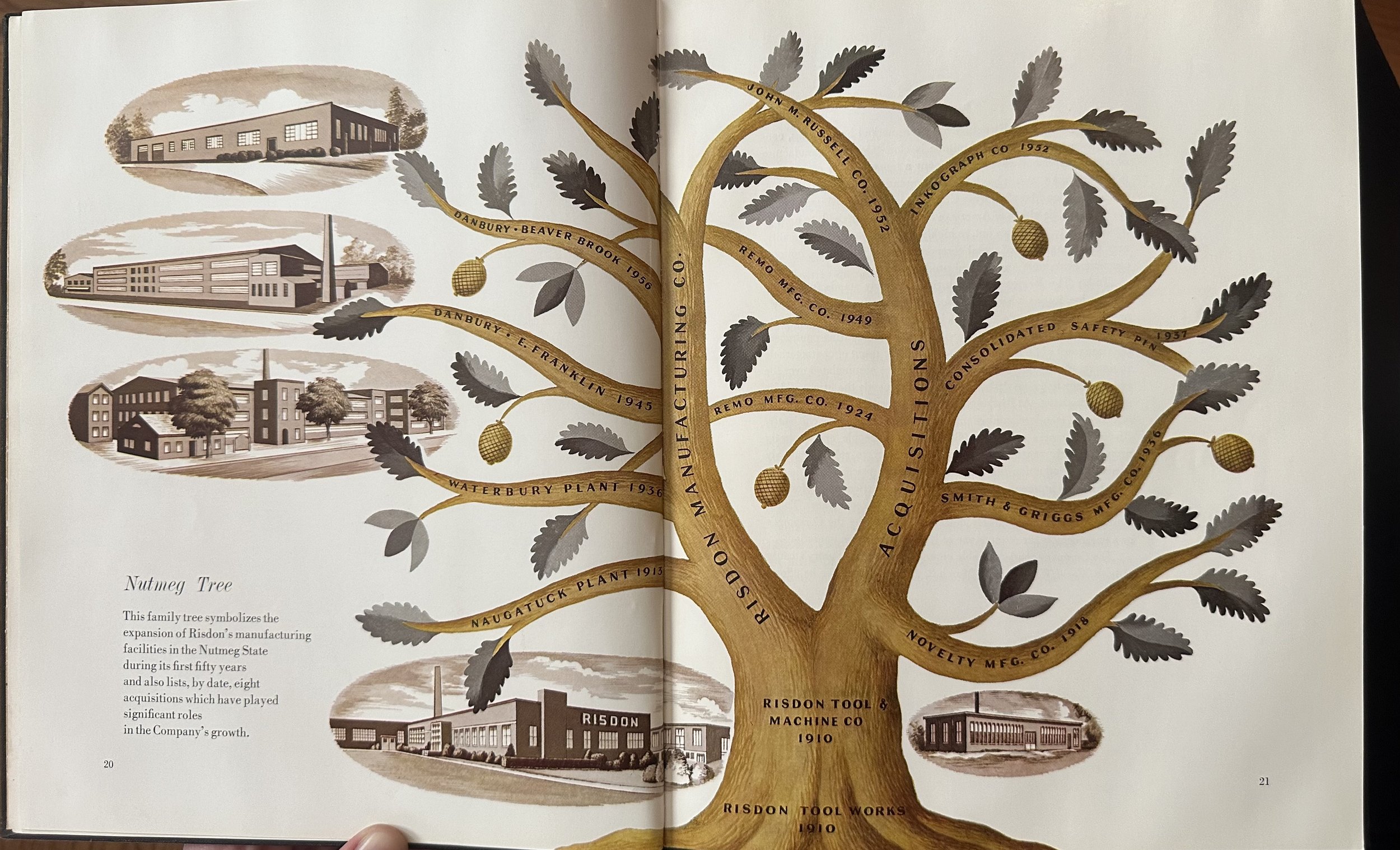
Source: Connecticut Enterprise - Risdon
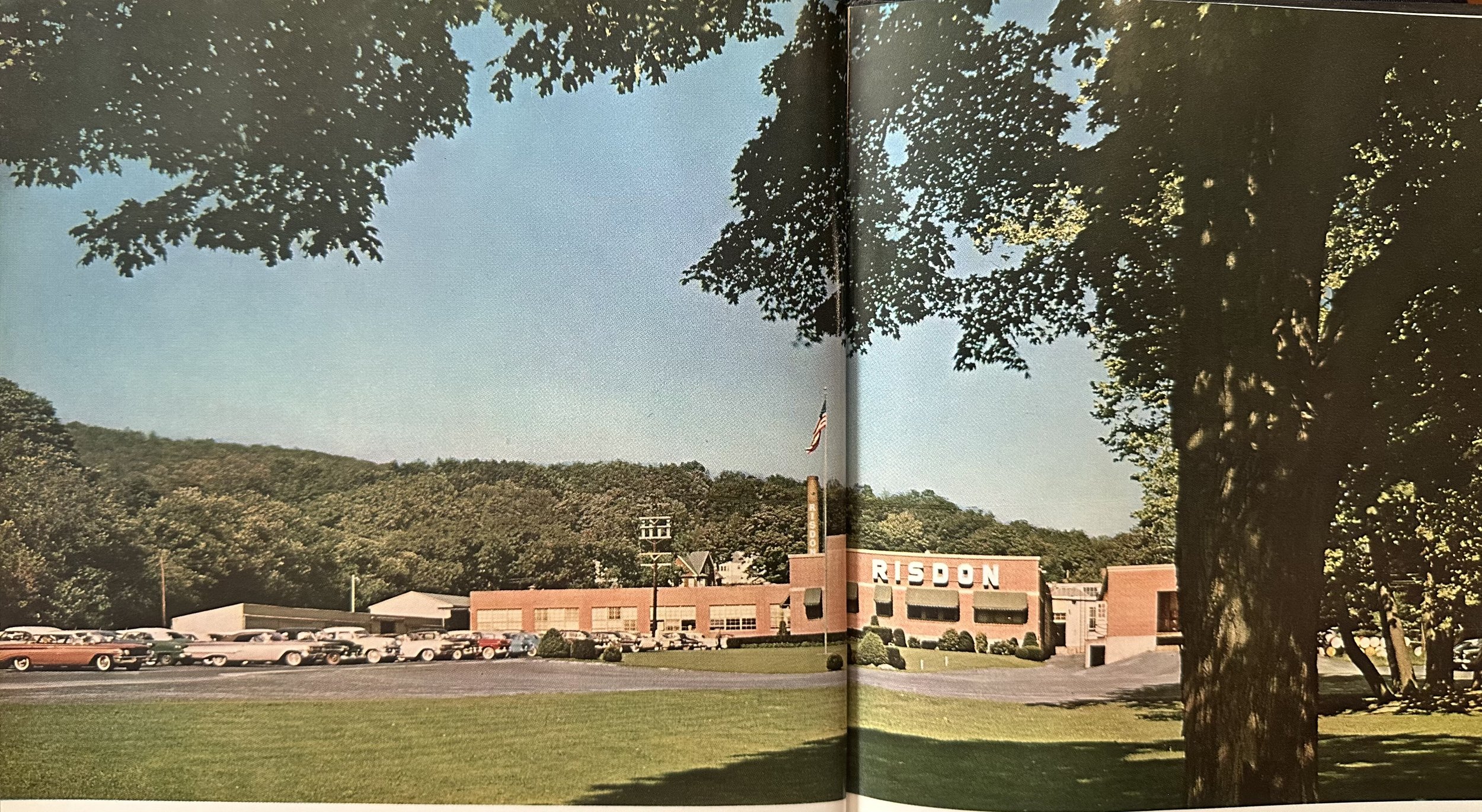
Naugatuck Plant - Source: Connecticut Enterprise - Risdon
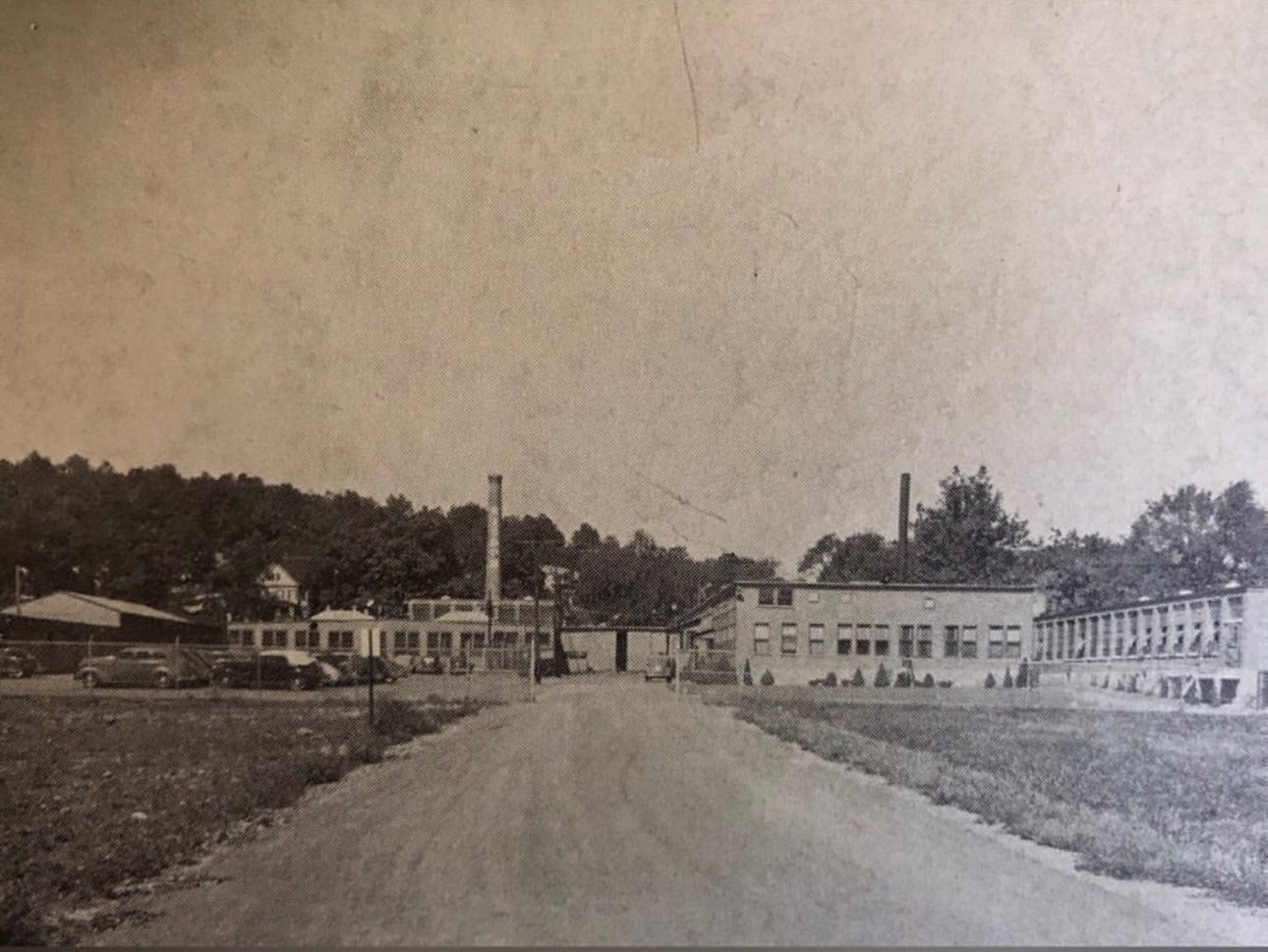
Undated
Online Research Library