Naugatuck Footwear Plant
Excerpt from Naugatuck Daily News – Monday, September 15, 1947
Industrial Exhibit Supplement
Naugatuck Footwear Makes Shoes To Fit Every Need
The United States Rubber Company’s Naugatuck Footwear Plants cover more than 40 acres and have 80 buildings. For over one hundred years many of the footwear items people use every day—at work and at play—have been made right here. And the variety of Naugatuck’s footwear products is increasing every day—there being a shoe made at the present time for practically every conceivable purpose. In this picture story you see some of the exceptional technical skill, science, planning, and fine craftsmanship needed to make Naugatuck Footwear products; you see some of the modern manufacturing methods and honest workmanship that have made Naugatuck Footwear famed for its quality.

Naugatuck Daily News – Monday, September 15, 1947
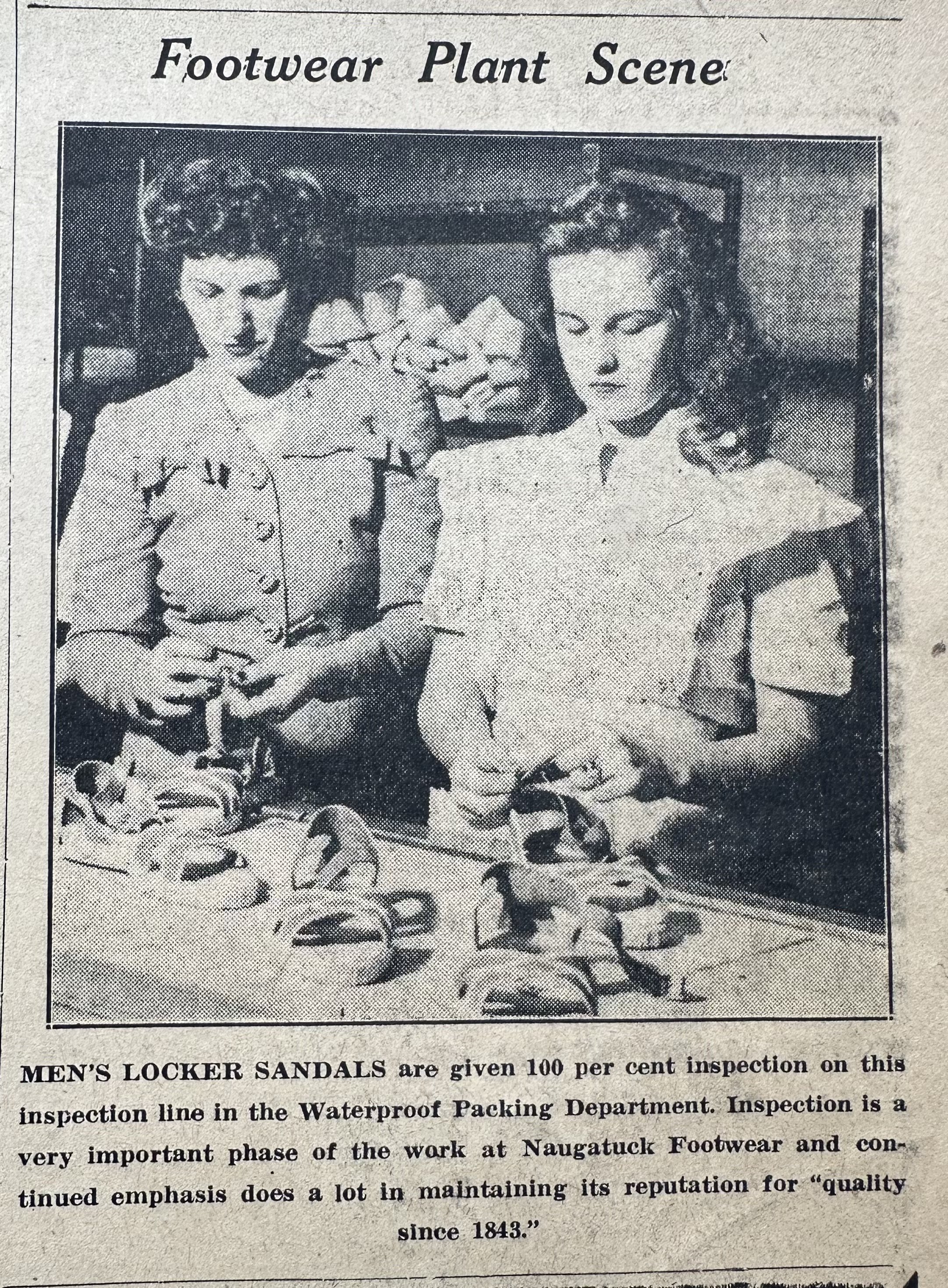
Naugatuck Daily News – Monday, September 15, 1947
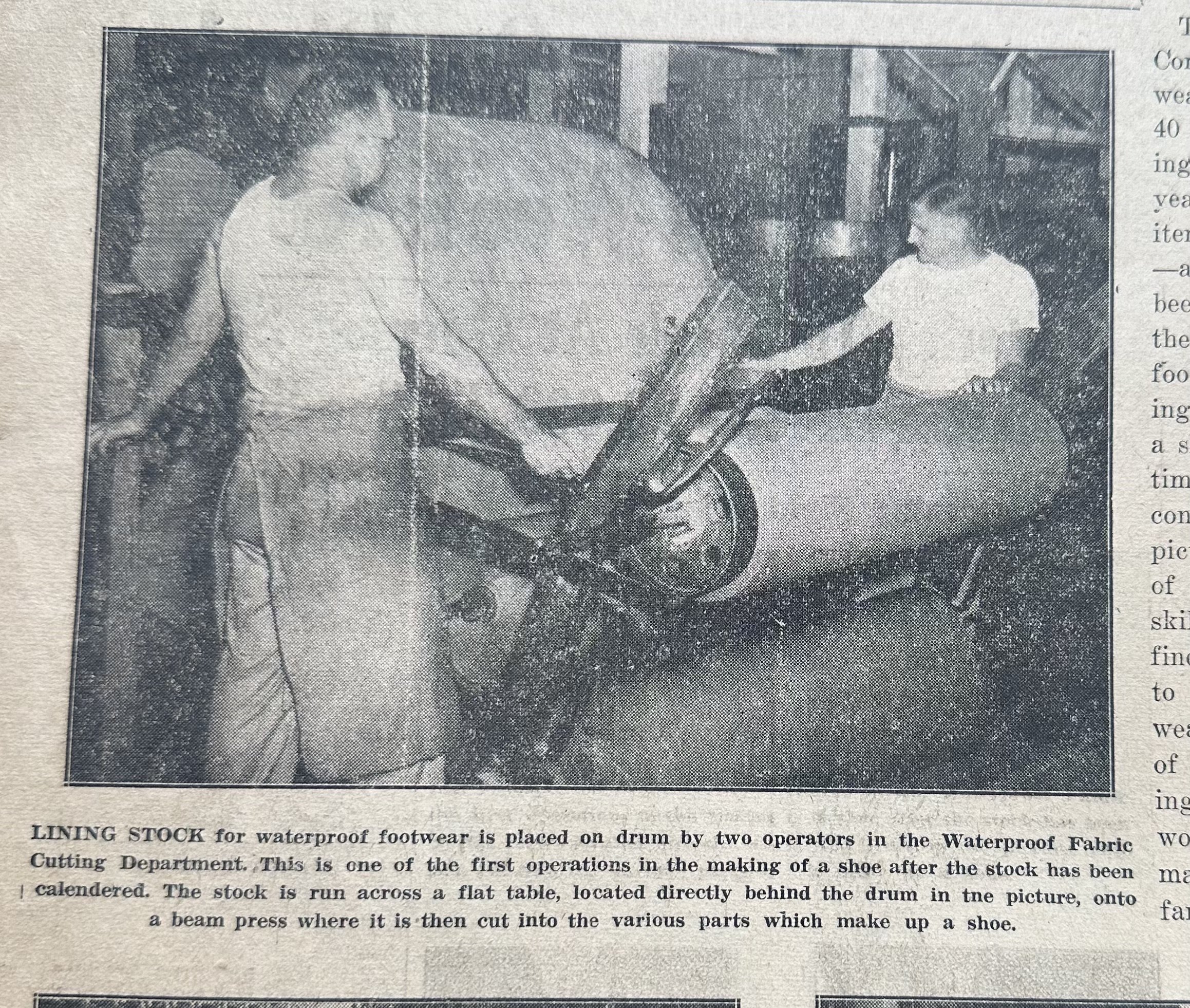
Naugatuck Daily News – Monday, September 15, 1947
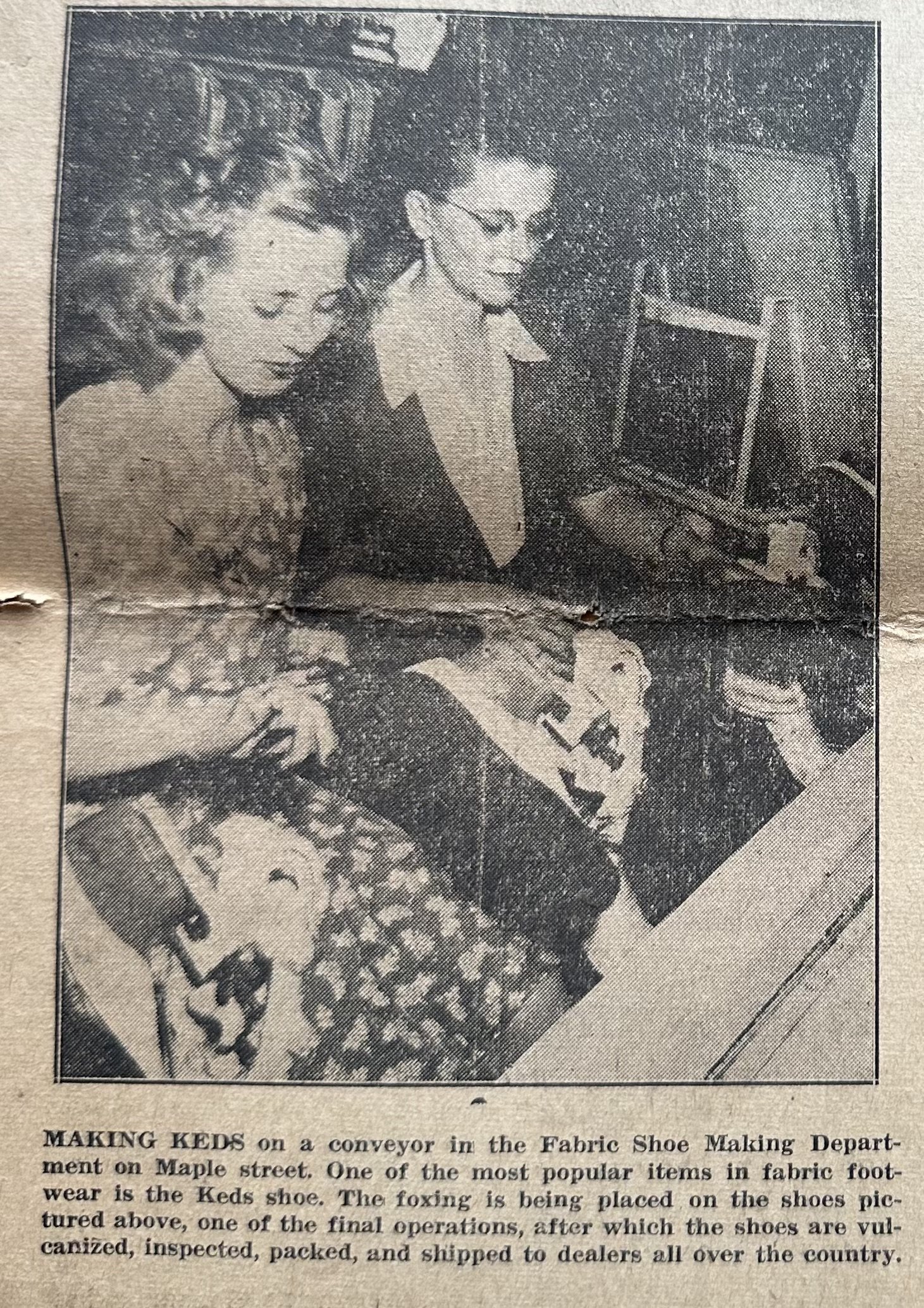
Naugatuck Daily News – Monday, September 15, 1947
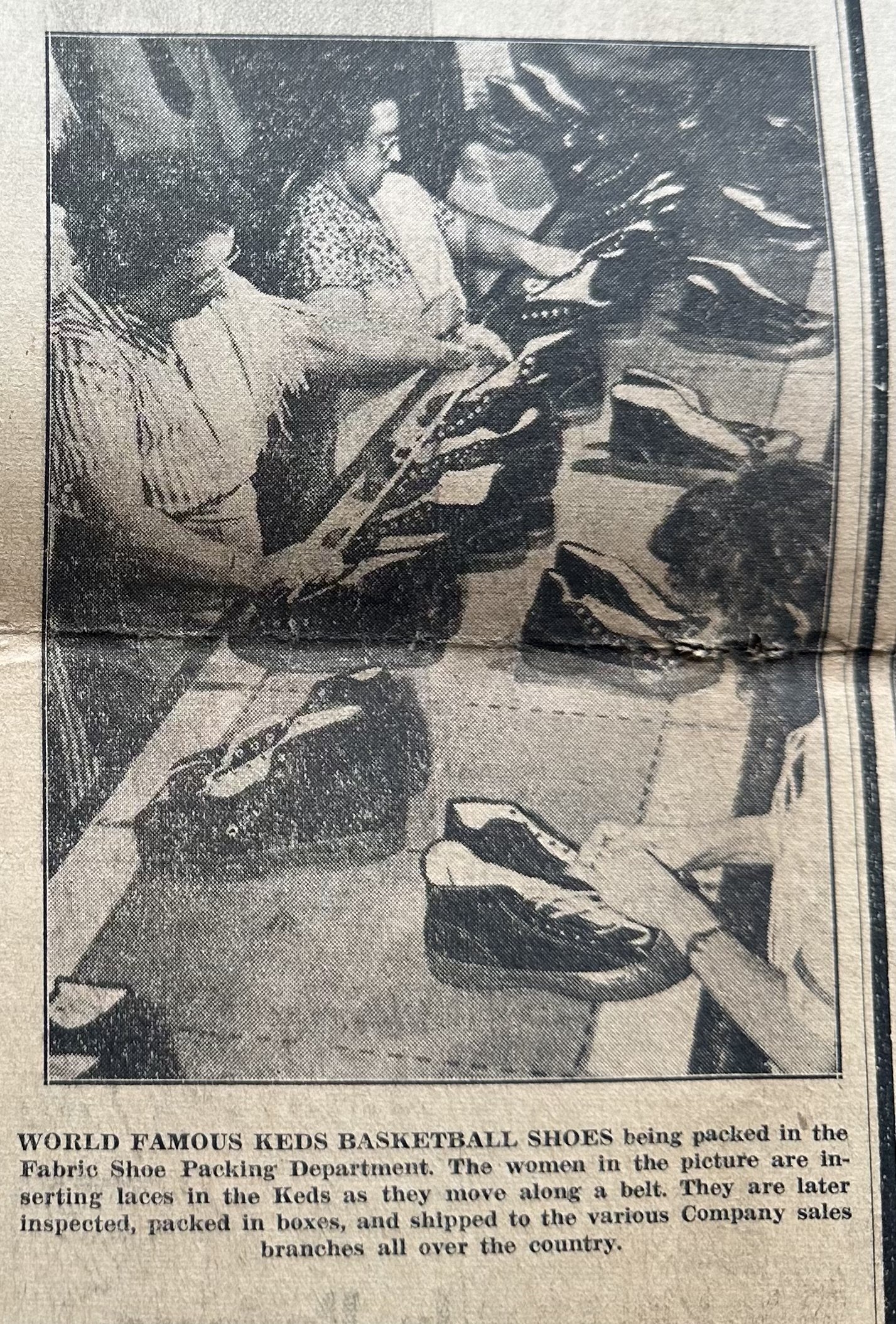
Naugatuck Daily News – Monday, September 15, 1947
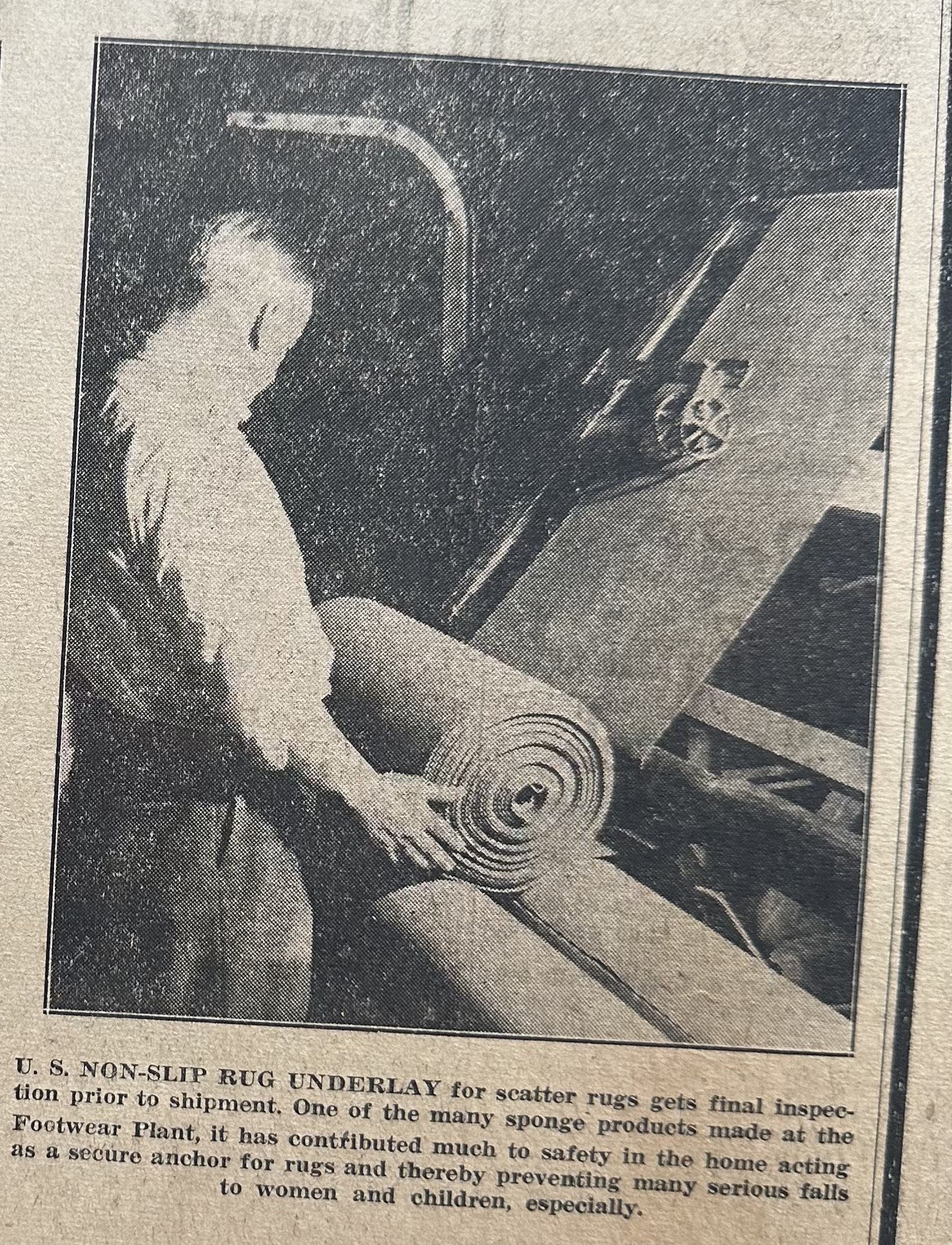
Naugatuck Daily News – Monday, September 15, 1947
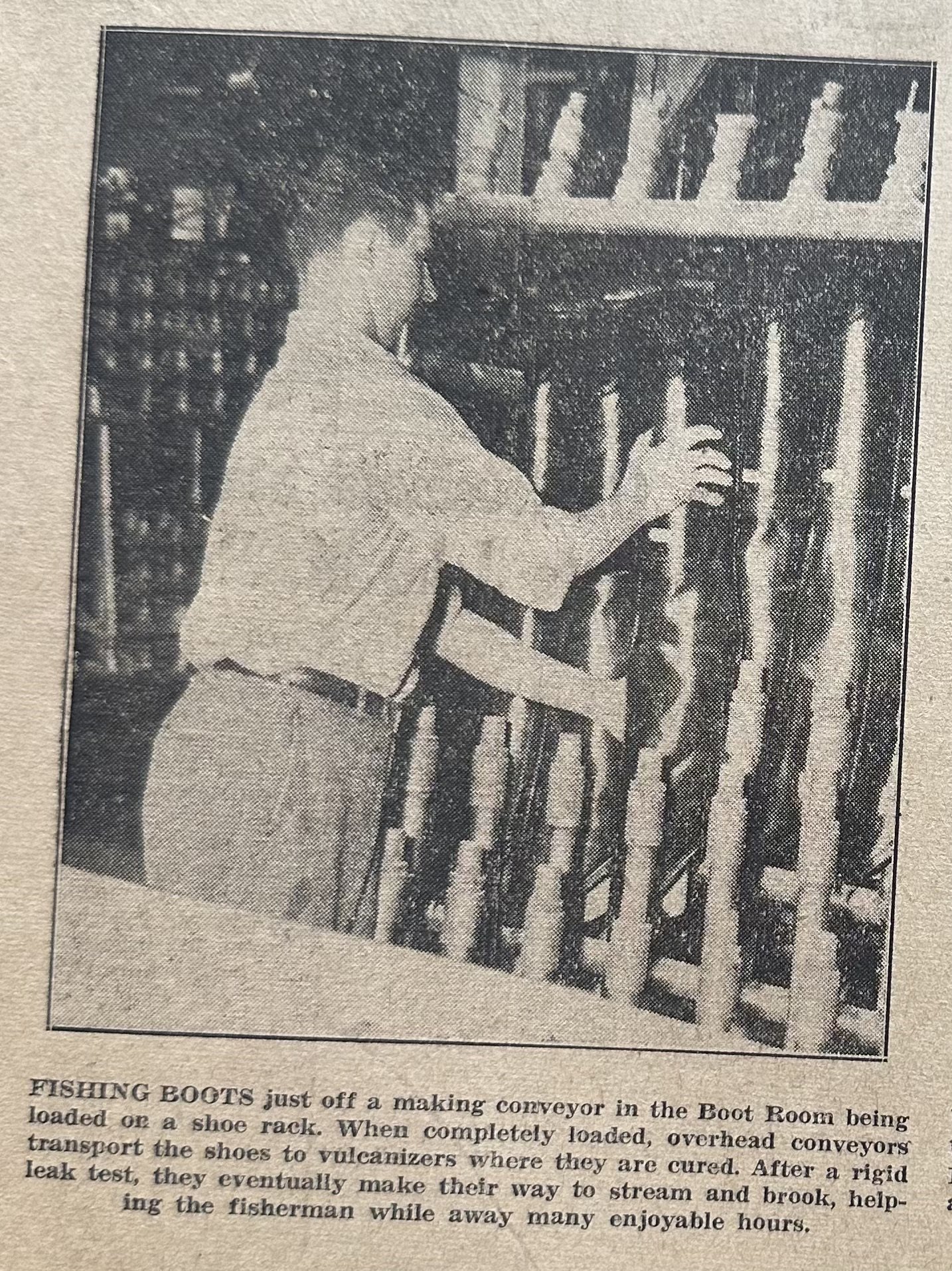
Naugatuck Daily News – Monday, September 15, 1947
Excerpt from Naugatuck Daily News – Saturday, August 31, 1946
World War II - History Edition
Footwear Plant First To Develop Many Products Of Vital Importance To All Branches Of The U. S. Fighting Forces
Fuel Cells Made Here Used In Famed Doolittle Raid On Tokyo
"Now it Can Be Told" might well be used as the title to this story describing the tremendous effort in many varied fields of war production which the Naugatuck Footwear Plant of the United States Rubber Company made as their contribution toward the successful conclusion of World War II. Only recently has the full story come to light, since a rigid degree of secrecy was maintained throughout the war years to prevent any vital information about their part from falling into enemy hands.
At the time of the United States entry into the war, the Naugatuck Plant was producing footwear and employing over 1,000 people, it turned out a complete line of canvas and waterproof footwear. During the war years, the Footwear Plant established an amazing production record on items it had never before manufactured, including storage tanks, life-saving suits, aviation suits, fuel cells (for nine different type planes), life-saving boats, barrage balloons, pontoons, and numerous special items of war footwear for the armed forces and for essential protective and occupational use. All of these items were vitally needed for furtherance of the war effort but, it is stressed, it was "life saving" and "health protecting" items rather than production of equipment designed to kill.
The conversion from civilian to war or government footwear was done quickly, and seemed relatively easy because of the efficient way the gigantic job was handled by the Rubber Company's engineers and development men. However, the problems which had to be met and solved were multitudinous. The dwindling supply of real rubber, the use of reclaim, and the development of synthetics made this period a particularly trying one.
The introduction of synthetics provided many problems. Thiokol had a nauseating odor. The synthetic rubber lacked the tackiness of crude rubber. This required numerous cementing operations which were likewise dirty and odorous.
The change from footwear production to cell, boat and pontoon production also presented a complexity of training differences. It meant the operators had to work with a much larger product than a shoe, they had to remember much more, they had to recognize the difference in parts that at first glance looked identical, and they had to repeat an operation whose cycle before repeating an operation was much greater. Constant changes in construction, undesirable jobs because of odor and cement, difficulty in getting rate standards on new work, and new operations meant constant training and retraining. After the first few months of trial and error, conditions improved to a great degree and, likewise, training took a more systematic turn.
Wartime Production
Swinging into full war-time production after the preliminary difficulties had been ironed out, it wasn’t long before the Footwear Plant’s valuable contribution to the war effort became evident in many ways. Surpassing all others, the local U. S. Rubber Plant was first in developing the following articles for the various branches of the armed services: All rubber four-buckle arctics for the Army; aviator wader for the Engineers’ corps; canvas climbing shoe for the army; canvas oxford “Sperry Sole” for the Amphibian Corps; decoy plane and five-man raft for the Air Corps; jungle boots for the Army & Marine Corps; leather top overs “Yukon” for the Army; leather top overs “Sperry Sole” for the Navy; life saving suits for the life saving suits for the Coast Guard and Army Transport; mukluks for the Army (cold climate); one-man parachute raft for the Army and Navy; poncho “Thiokol” reconnaissance boat “Thiokol” and rubber wader-man suit for the Air Corps; seven-man raft for the Air Corps; seven-man raft for Navy and Army Transport; “Storm King” boot for the Navy; fifteen-man raft for the Air Corps; fifteen-man raft for the Navy; barrage balloons for the Navy and Army and an asbestos heater balloon for the Air Corps; shoes for the Air Corps; “Buna S” reconnaissance boat and kite for the Army.
Barrage Balloons
Early in February 1941, the Naugatuck Footwear Engineering Department organized a balloon drafting group and preliminary drawings for Barrage Balloons. An educational order for four balloons was placed with Naugatuck by Wright Field in May.
Preliminary trial run of neoprene-coated balloon fabric was successfully carried out. Factory trials carried out during the next two months obtained satisfactory storage grading and handling methods for balloon fabrics. On August 13, the first balloon was tested at the Yale Field House in New Haven. Additional improvements were made as a result of this test and by October the stage was set for full scale production which, it had been previously decided, would be carried on at the company’s Woonsocket Plant. It is interesting to note that the barrage balloons, developed in Naugatuck and made in Woonsocket, were used along the coast of California as a part of the coastal defense against Japanese planes during the time they were operating in that area.
The Ponton Department started early in May 1942 and was discontinued the following January. It employed about 150 people at its peak and turned out sixteen pontoons a day at its production high point. Pontoons, or Pneumatic Floats, as they were later referred to by the Army Engineers, were first made out of Thiokol and then from Buna S. These floats, with a carrying capacity of 10 tons, were used to good advantage in building bridges across rivers when our armies were chasing the Germans through France and back into Germany.
Boats
The Boat Department also started operations early in May 1942. Production reached a high of 60 boats a day and peak employment reached about 150. The pneumatic boats produced in Naugatuck were made from sturdy fabrics with relatively heavy coatings of rubber and many reinforced patches, and was so constructed to resist constant shoe scuffing and repeated wear. The boats were built as ruggedly as possible without completely losing sight of the inherent advantages of light weight and portability. They found wide application in the Armed Forces.
Morner Suits
The first Life Saving Suit, the so-called “Morner Suit,” was made at Naugatuck in December 1941. The suits were tested in the local Y.M.C.A. swimming pool. Production was on a very small scale at the outset but when the conveyor method of manufacture was started in May 1942, production was increased from 112 suits to almost 1500 suits per day. These life saving suits were used to best advantage by the crews of merchant vessels, Coast Guard ships, tenders, and by Navy fighter pilots. The real value of life saving suits was forcefully brought out in the early days of the war when our oil tankers, lacking the proper convoy protection, were being sunk at an alarming rate by prowling German submarines. As the sinking of ships increased and the loss of life grew correspondingly greater, it came to a stage where the crews refused to man the tankers until suitable life-saving suits were provided. At this point, the government called upon the U. S. Rubber Company to provide a life-saving suit in sufficient quantities.
Fuel Cells
The Fuel Cell Department was by far the largest of those departments engaged in special war production. These self-sealing gasoline tanks, as installed in the fuselage and wings of all type aircraft, both large and small, undoubtedly saved innumerable lives and were an outstanding development as they affected the air service branch.
Employing almost 1,000 people at its peak, the Fuel Cell Department occupied practically the entire Fabric Shoe portion of the Footwear Plant’s facilities. Fuel cells were built on plaster forms, with layers of fabric and the cord piled up much in the same manner as a tire. After vulcanization and various finishing operations, the cells were shipped for assembly in the many different types of fighter craft. Each model airplane used a different size and shape cell. From the time the first fuel cell was completed in the latter part of October 1941 until shortly after V-J Day, when production came to a halt, a total of approximately 78,000 fuel cells were turned out by the Naugatuck Footwear Plant. The cells were assembled in United States Army and Navy planes which saw service in every corner of the world, including such famous makes as the B-24 “Liberator” bomber, manufactured by Ford; the P-47 “Thunderbolt” fighter, manufactured by Republic Aircraft; the F6F “Hellcat,” F7F “Wildcat” and F8F “Tigercat,” fighter planes produced by Grumman Aircraft A30A “Baltimore” bomber, made by Glen L. Martin, and the F4U “Corsair” fighter, turned out by Chance-Vought in Stratford, Conn.
An interesting story in connection with fuel cells was the revelation of how they figured in the first flight of General Jimmy Doolittle’s squadron over Tokyo early in the war. As everyone remembers, it was a surprise attack on Tokyo, the planes taking off from the U. S. Aircraft Carrier Hornet while still many miles away from their objectives.
The fact that each plane was equipped with a collapsible fuel cell, developed in Naugatuck and produced in the Mishawaka Plant of the U. S. Rubber Co., gave the plane extra flying distance and enabled them to accomplish the daring mission.
Decoys
Decoy targets, developed in Naugatuck and produced entirely in the Woonsocket Plant of the Rubber Company, were another item which proved to be of inestimable value in combat operations. Production was carried on behind locked doors and strict secrecy was maintained. When the full story came out after the war, it was an amazing revelation—of how a so-called “Sleeping Beauty” army, made up of truckloads of tanks, guns, and other military paraphernalia, were inflated to simulate divisions of thousands of men. The fake tanks and guns were sent into “action” with the playing of sound effects reproducing the noises of clanking tanks and roaring guns. Built mostly of large-sized pneumatic tubing, the fake equipment, when blown up, could not be told from the real thing at 20 feet away.
The rubber army, operated by little more than a thousand specially-trained United States Army Engineers, was credited with playing an important role in baffling the Germans with tricky diversionary maneuvers designed to draw off the enemy from sections where real attacks were to be launched. It was first tried out in the Normandy invasion that proved so successful and that it saw action in practically every important campaign in subsequent operations, including St. Lo, the battles for Paris, Brest and Luxembourg, the Saar campaign and the Rhine crossing.
Built to look exactly like regulation lightweight tanks, medium tanks, 90 mm., 105 mm., 120 mm. and 155 mm. guns, the equipment was easy to send to combat areas because it was collapsible. For compactity, could be inflated quickly in combat zones, and deflated just as quickly for swift movement to a new location.
Usefulness of the targets depended upon the large-sized pneumatic rubber tubing. Speed was so essential that when shipments of the more live items that produced in Woonsocket was stepped up until the output was quadrupled with 10 divisions being turned out daily, in addition to the finished decoy targets.
Although these items had never been manufactured before and had to be engineered from scratch, the Engineers’ Corps was so pleased with the aid given them in this problem, and particularly the speed with which the U. S. Rubber Company was able to accomplish their aims, that Woonsocket was asked to take the entire order, subsequent to this and overseeing their construction by other manufacturers as necessary.
Although it might appear from the story thus far that the production of rubber footwear during the war was virtually eliminated in the Naugatuck Plant, such was far from being the case. Over 1500 people were busily engaged during the entire period turning out the highest quality canvas and waterproof footwear for which Naugatuck has become famous during the past 100 years, only in this instance over 90 per cent of their productive effort went to some branch of the armed services.
A few figures are given to illustrate the Footwear Plant’s vast contribution to the winning of the war alone. A total of over 1,200,000 boots of many different types were provided for all branches of the service. More than 3,000,000 rubbers and over 2,000,000 arctics were turned out for Army and Navy use. The army infantry was provided with 650,000 Leather Top Overs. An astronomical figure of approximately 6,500,000 Canvas Shoes were produced for the different service branches. Included in this latter figure were jungle boots and other canvas type shoes worn for both service and sports wear.
Although space does not permit a description of all the different type footwear produced at Naugatuck, and their valuable application on the field of battle, mention is made of a few of the widely-used types. Produced especially for the army were the following: Canvas Climbing Shoe, a molded sole type of shoe built along the lines of a basketball shoe with a canvas tin; Leather Top Overs “Yukons”; Cold Weather Boot, designed so it could be worn over several pairs of heavy socks and felt insoles; Four-Buckle Cashmerette Gaiter, constructed to be worn over shoes in temperatures down to 10 degrees below zero, and without shoes but with several pairs of socks in lower temperatures.
Designed especially for the Navy were: The N1 Sea Boot, a leggin boot with soft, collapsible upper made for cold climate use in submarines and worn over several pairs of wool socks, and a duffel sock along with two pairs of insoles; Firefighter Boot, used in fighting fires and having a sole which would not burn readily yet retaining its non-skid feature; Submarine Boot, which was used by men on watch on submarines in northern waters.
Developed for both Army and Navy use were a Short Snug Ankle Boot, a Hip “Storm King” Boot, and a Short Heavy Boot. The Amphibian Corps was supplied with a Canvas Oxford “Sperry Sole” which was born to prevent slipping or skidding on smooth surfaces, such as boat decks, airplane wings, etc.
Furnished to Cold Climate Troops were Mukluks, having a special type of rubber bottom with canvas or rubber tops which were worn over several pairs of heavy socks in cold climate. A special shoe, the Jungle Boot, was furnished to both the Army and Marines for jungle wear. The Engineers’ Corps were also taken care of with an Aviator Wader, a coverall type of boot with built-in air chambers capable of being blown up by mouth to provide buoyancy.
Leaving the production record and turning to the moral building activities—for the United States Rubber Co. Footwear Plant, like other corporations in industry, the most critical problem during the war was for production which resulted in the attendant labor management problems of manpower, absenteeism, labor turnover, shop discipline, long hours of work, drafting of key men, and the indoctrination of new employees under before exposed to industrial employment. The problem of absenteeism was the worse bug-a-boo for both management and labor due to the long schedule of hours and the attendant Sunday and holiday work.
The Footwear Plant was one of the first concerns in the area to organize labor-management committees as a teamwork approach to getting production on an unbelievable scale. These groups took an active part in the sale of war bonds, together with Red Cross and Community Service Drives, to keep the Company in the vanguard of homefront services.
The Labor-Management Committee, as organized early in 1942, was comprised of fourteen members—seven representing labor and seven representing management. Two co-chairmen were selected, the one for labor being Joseph P. Kinisea, President of Local No. 45, and the other Harry L. Carter, representing management.
E Award
In one of the most colorful ceremonies ever held in Naugatuck, the Footwear Plant was presented with the Army-Navy E Production Award on December 29, 1943. The program was held on the fourth floor of Building 216 and was broadcast over the Connecticut network.
R. E. Lowell, Industrial Relations Manager, acted as Master of Ceremonies and introduced the long list of distinguished visitors, both military and civilian. The featured speaker for the event was Herbert E. Smith, President of the United States Rubber Company, who was making his first appearance in Naugatuck. The ceremony, witnessed by almost 5,000 people, will long be remembered in Naugatuck as a glowing tribute to the fine job the employees of the Footwear Plant had been contributing to the war effort.
On September 18, 1944, an additional award of a star for the Army-Navy E-banner was bestowed upon the Footwear Plant for continued excellence in the production of war materials.
War Bonds
An almost continuous campaign was carried on to encourage the purchase of War Bonds from the time when they were first placed on sale by the United States Government. Early in the drive, the Footwear Plant exceeded 100 percent participation of employees buying Bonds through payroll deductions and were thereby awarded the Minute Man Flag by the Treasury Department. Throughout the war an average of approximately 90 percent of the total plant payroll was being put into the purchase of Bonds. For a considerable period, also, a 100 percent employee participation was maintained in the payroll savings plan.
Service Record
Almost 1,000 men and women left the service of the United States Rubber Co. Footwear Plant to enter the armed forces, of which 27 made the supreme sacrifice. Every branch of the service in every front of the war found former Naugatuck Footwear employees fighting for their country.
Reconversion problems at the Footwear Plant were practically non-existent. Here the problem was one of need for more production workers since manufacture of civilian products require more operations than did manufacture of materials for war.
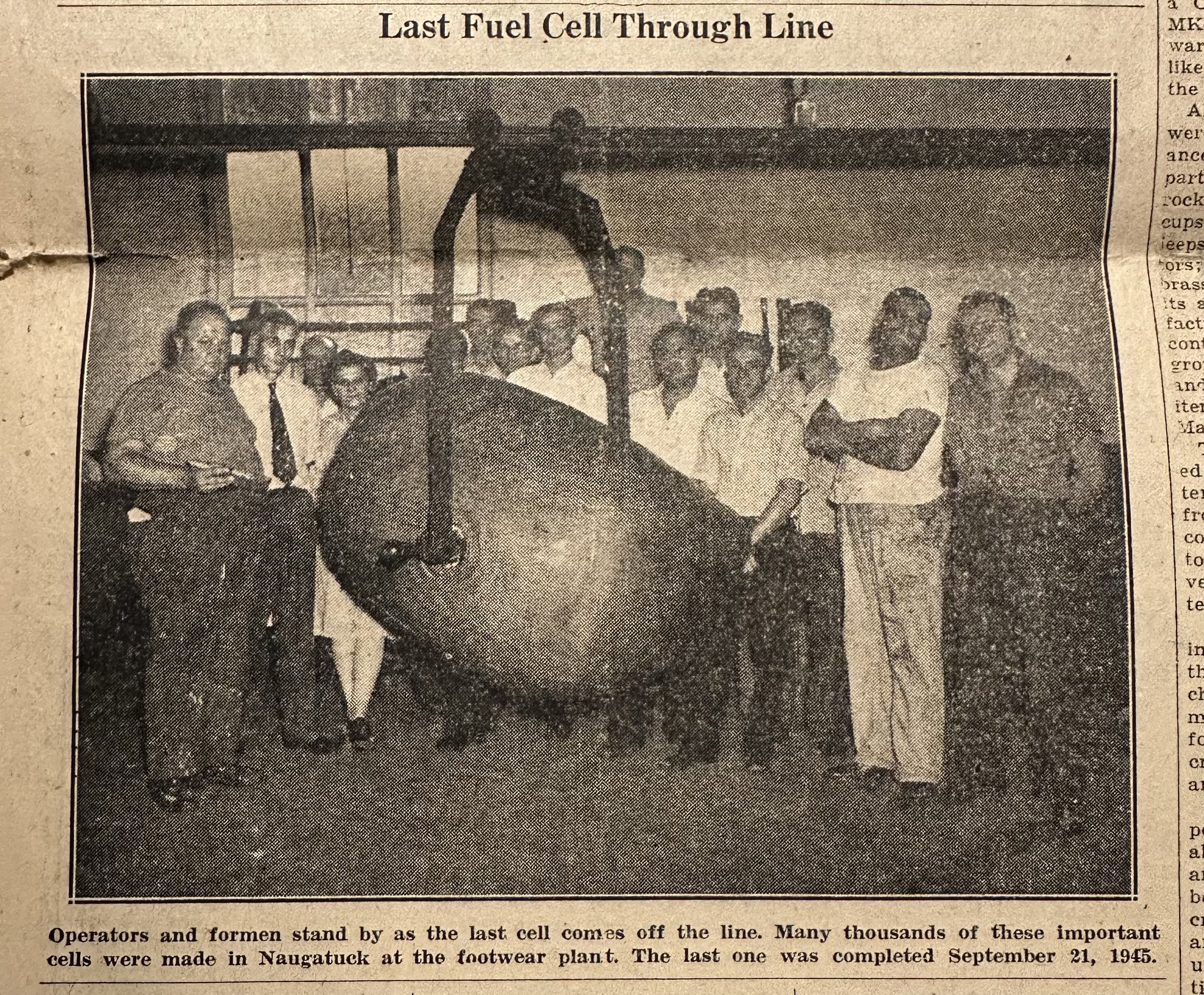
Naugatuck Daily News – Saturday, August 31, 1946World War II - History Edition
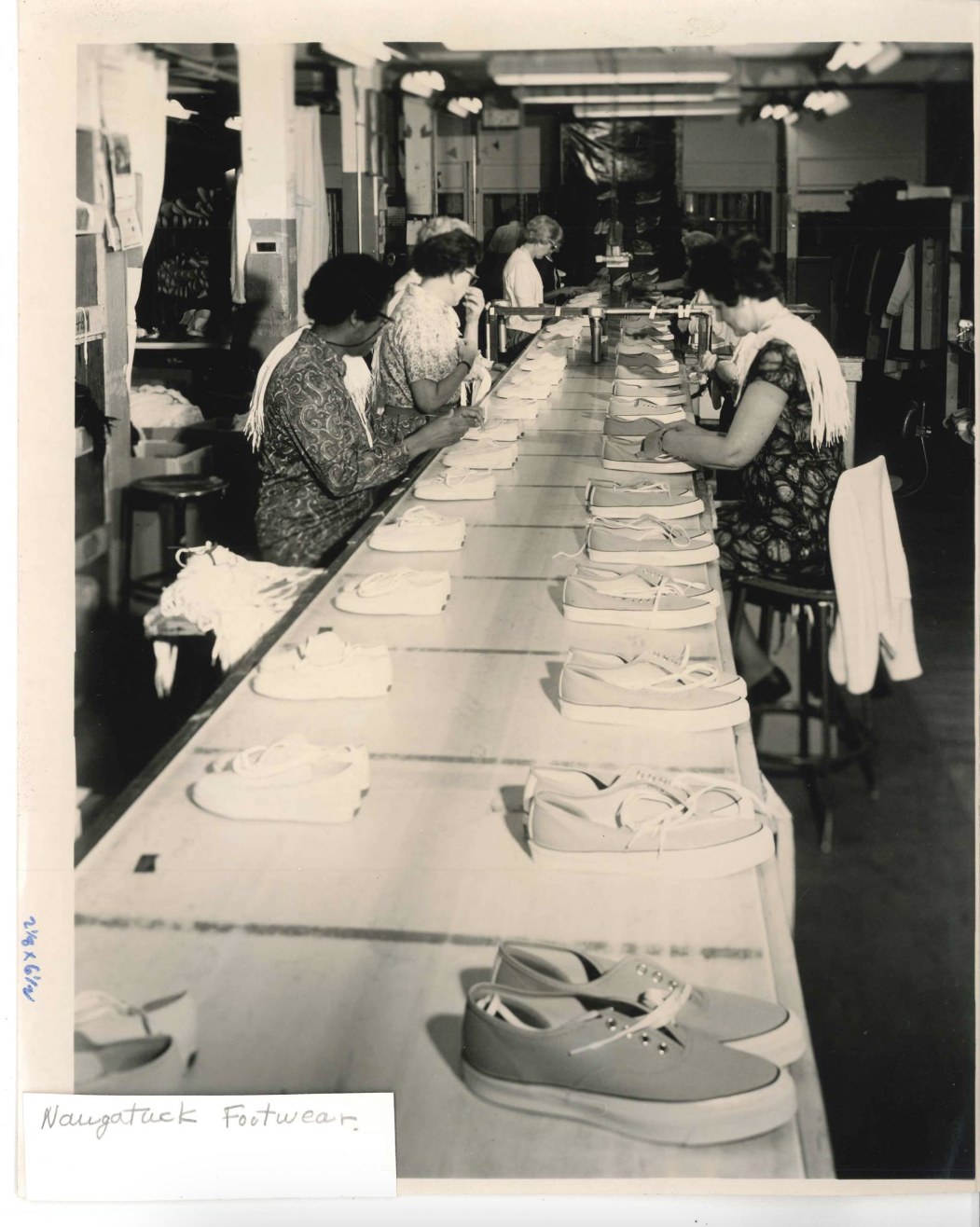